Sector - Commercial Aerospace
Project – Revolutionising the Aircraft Product Change Management System
Aims - Mapping business processes, reorganising teams, reducing waste and transforming effective management decision making systems, and getting better results from multidisciplinary teamwork
What was involved?
A multi-disciplinary working group was set up to define the aircraft product change processes. Subsequently, a multi-disciplinary product change management team was established, to own the end-to-end business process and to more effectively coordinate and run modification activities.
This including new modifications requests, repercussion assessments, budget management and monitoring of progress to revised process management criteria and KPI’s
This Business Process Team drove massive savings in both efficiency and effectiveness, as well as significant waste reduction, with many novel improvements linking strategic requirements to tactical implementations…
The team designed and implemented a new modification prioritisation system for 500+ live modification requests in ‘the system’, with approximate value circa £30M and more effectively managed a smaller £12M pa design budget, to achieve best value for money spent.
The Mod Prioritisation System translated strategic product change demands into practical decision making discussions, enabling competing and conflicting change requests to be effectively ranked in a systematic way, with consistent input from all parties and reducing infighting over most favoured modifications.
The Change Management Team reduced the previously ‘normal’ organisational conflicts and the distractions of competing ‘vested interests’, which governed the old system of modification proposal assessment and decision making
Huge improvements to the quality of management team decision making for modification go/no go authorisations whereby authorised modifications entered a queueing system, pending annual budget constraints, before agreeing target aircraft set embodiment decisions.
The new change team business processes and systems innovations were shared across the British Aerospace plc group
The new product change process and teamwork innovations were recognised as ‘International Best Practice for Product Change Management’ by an external, US based Configuration Management II Institute.
What the client said…
“The ATP Change Management Team has significantly improved the way we manage and control modifications and changes to our product specifications and customer deliverables, throughout both manufacturing build cycles and in-service modification programmes. It represents a step change in our multi-disciplinary team working approaches and management control systems, enabling better value for money to be delivered, for both ourselves and our customers, within tight development budget constraints.”
Mike Taylor, Head of Project Management (Advanced TurboProp) BAe Regional Aircraft
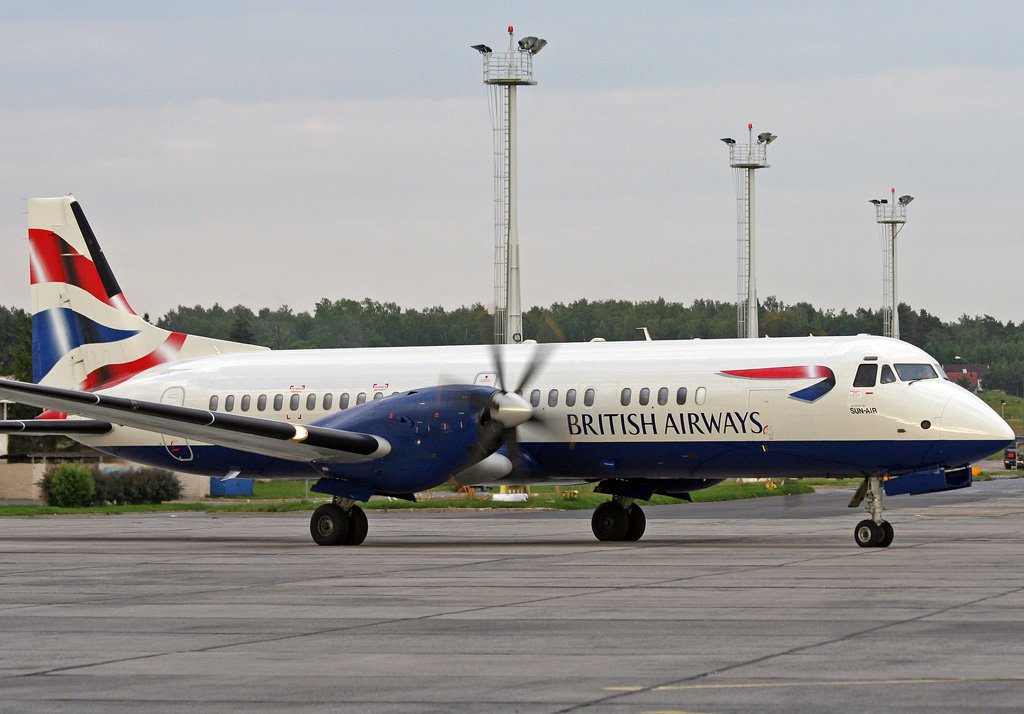
